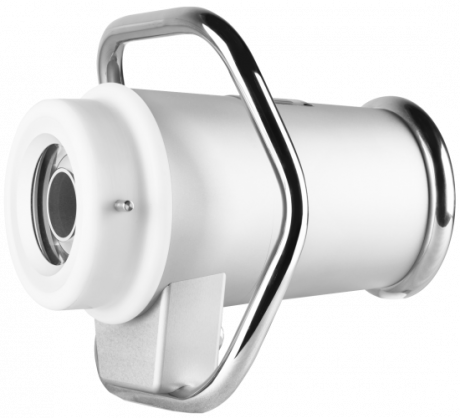
Patvis APA
Process Analytical Technology Visual Inspection System for Automated Particle Analysis
PATVIS APA is designed for real-time visualization, monitoring and diagnostics of process development, scale-up, transfer and production.
There are three levels of PATVIS APA operation (visualize, measure, control) and you choose the level of leveraging the acquired visual information of the process, delivering the benefts of quality by design.
- Monitoring batch-to-batch reproducibility
- Size and shape information in real-time
- In-line, at-line or off-line mode
- Noninvasive and contactless
- Portable, ergonomic and tool-free
- Intuitive graphical user interface
- Telecentric optical system
- ATEX compliant
Visualize, measure, control
PATVIS APA is designed for real-time visualization, monitoring and diagnostics of process development, scale-up, transfer and production. There are three levels of PATVIS APA operation and you choose the level of leveraging the acquired visual information of the process, delivering the benefits of quality by design.
Live view
Mounted directly on process equipment, PATVIS APA provides a live view of the product. A high-speed camera with a telecentric optical system assures noninvasive acquisiton of detailed images for clear visualisation. Live view allows saving of all images of the process for later qualitative or quantitative analysis, which is especially useful for in-process product behavior observation and better process understanding.
Real-Time Measurements
PATVIS APA offers accurate measurements of CPP‘s with exceptional particle rate and excellent statistical strength in real-time, which is key to process optimisation. Proprietary and speed-optimised image analysis algorithms provide numerical data through an intuitive graphical user interface for immediate process feedback.
Process Control
PATVIS APA offers software compliance to GAMP and FDA requirements and can be integrated with interfaces of production equipment for increased autonomy with automatic process monitoring, alarming and control.
Fluid bed coating
Coating process
Pellets are typically drug-loaded with API (layering) or film-coated to modify the API release kinetics, thereby achieving delayed or extended release. Characteristics of coated pellets, such as Pellet coating thickness and Pellet agglomerate fraction, are critical process parameters that determine the process performance in terms of product quality, product yield and production time.
Coating thickness
Precise coating thickness control is rapidly gaining importance with an increasing amount of modified release formulations on the market. Drug release and drug loading are characterized by the thickness of the coat. PATVIS APA enables coating thickness estimation based on particle size increase even for thin film coatings on pellets and minitablets. The coating process can be terminated reproducibly when the desired end coating thickness is obtained.
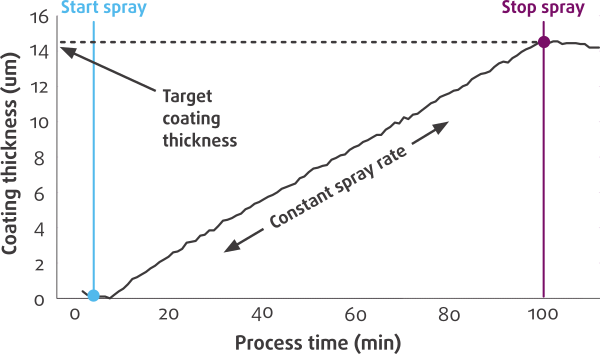
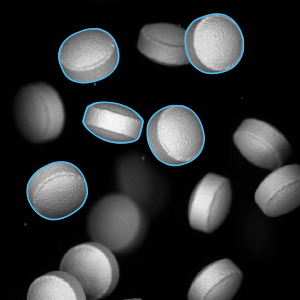
Agglomeration
Pellet agglomeration is an inevitable property of the coating process. Obtained agglomerates are a common cause for process down time and directly affect the final product yield and coat integrity. PATVIS APA enables early agglomeration detection with visual confirmation of agglomerates. Quantification of the amount of agglomerates in the process provides means for timely intervention. In this way, agglomeration can be tightly controlled.
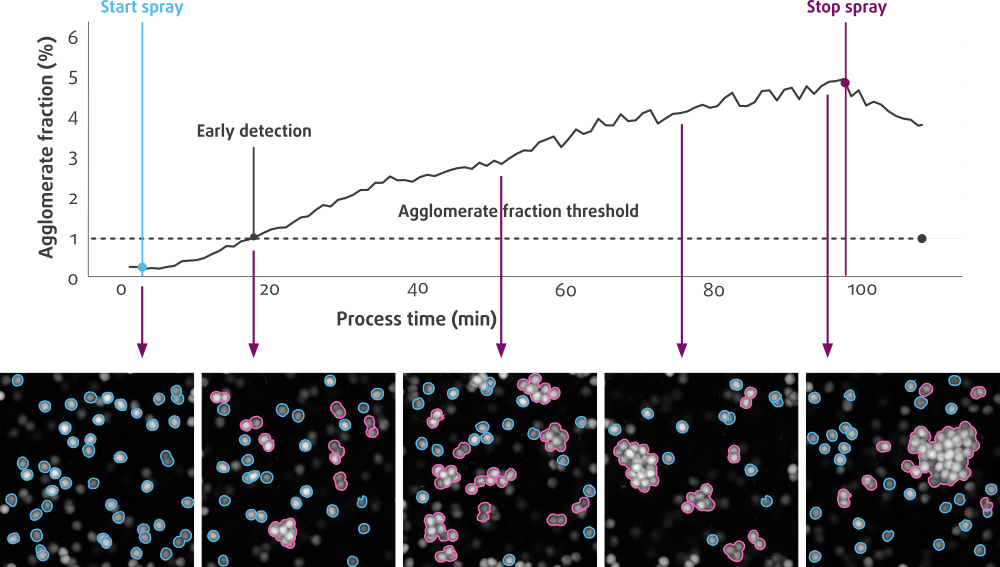
Technical data
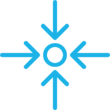
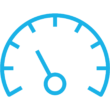
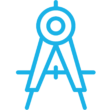
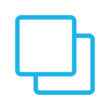
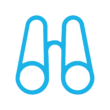
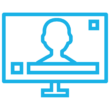
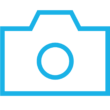
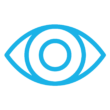
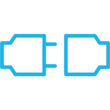
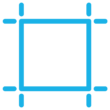
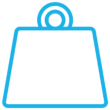
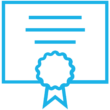
Video
Publications
Scientific Articles
Oman Kadunc N, Šibanc R, Dreu R, Likar B, Tomaževič D.
In-line monitoring of pellet coating thickness growth by means of visual imaging. International Journal of Pharmaceutics. 2014 Aug 15;470(1):8–14.
https://doi.org/10.1016/j.ijpharm.2014.04.066
Mehle A, Kitak D, Podrekar G, Likar B, Tomaževič D.
In-line agglomeration degree estimation in fluidized bed pellet coating processes using visual imaging. International Journal of Pharmaceutics. 2018 Jul 30;546(1):78–85.
https://doi.org/10.1016/j.ijpharm.2018.05.024
Gregor Podrekar, Domen Kitak, Andraž Mehle, Domen Rački, Rok Dreu, and Dejan Tomaževič
3D Orientation Estimation of Pharmaceutical Minitablets with Convolutional Neural Network. In 2019 15 International Work-Conference on Artificial Neural Networks, IWANN 2019: Advances in Computational Intelligence, 208-219, 2019.
https://link.springer.com/chapter/10.1007/978-3-030-20518-8_18
Nemanja Aničić, Polona Smrdel, Domen Kitak, Teo Morožin, Miha Jaklič, Peter Usenik, and Sara Vidovič
Applicability of Image Analysis to Support QbD Driven Development of Pellets. Drug Development and Industrial Pharmacy 47, no. 11 (2 November 2021): 1794–1808.
Podrekar G, Kitak D, Mehle A, Lavrič Z, Likar B, Tomaževič D, et al.
In-Line Film Coating Thickness Estimation of Minitablets in a Fluid-Bed Coating Equipment. AAPS PharmSciTech. 2018 Nov;19(8):3440–53.
https://doi.org/10.1208/s12249-018-1186-x
Korasa K, Vrečer F.
A study on the applicability of multiple process analysers in the production of coated pellets. International Journal of Pharmaceutics. 2019 Apr 5;560:261–72.
https://doi.org/10.1016/j.ijpharm.2019.01.069
Andraž Mehle, Boštjan Likar, and Dejan Tomaževič
In-Line Recognition of Agglomerated Pharmaceutical Pellets with Density-Based Clustering and Convolutional Neural Network. In 2017 Fifteenth IAPR International Conference on Machine Vision Applications (MVA), 9–12, 2017.
https://doi.org/10.23919/MVA.2017.7986760
Brezovar Teja, Svetič Sandi, and Dreu Rok
Comparison of the Robustness of Pellet Film Coating with and without In-Process Coating Thickness Evaluation. Pharmaceutics. 2022 Nov;14(11):2274.
https://doi.org/10.3390/pharmaceutics14112274