Even today, we still often compare machines to humans. The greatest contribution of machine vision compared to human vision is undoubtedly the reliability, repeatability and quality of the inspection. What does that really mean? Let’s have a look at a few risks, that we people have while performing manual inspection of tablets, capsules and softgels.
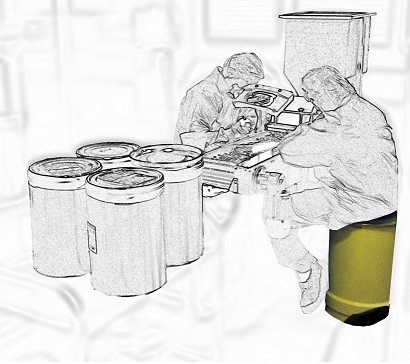
There are also “semi-automatic” inspection machines, that have a conveyor belt and light. This is still considered manual inspection, since inspection and sorting are done manually by people. By the way, why do people in this process sit on barrels so often? We’ve seen this all around the globe!
1. Focus is a limited resource! The quality of manual inspection will deteriorate over time because we get tired. The machines can perform reliable inspections around the clock with known risks that can be foreseen and minimized if operated properly. For example, if the product is dusty and the dust obscures the optical system, the machine inspection may also deteriorate. However, the deterioration in machine inspection is different from that of humans. We, are more likely to overlook defects (even critical ones) when we get tired. On the other hand, if there is a deterioration of the vision system (e.g. due to dust), properly designed vision systems will have “controls” built in to detect a possible deterioration and to prevent any defects slipping by.
2. Sensitivity hates speed. Human can be quite sensitive to small defects. Typically, at a distance of about 20-25 cm from the eyes, when the object is stationary, we can detect defects of 60-75 µm. If the described criteria are not met, our sensitivity can easily be reduced tenfold. The sensitivity of machines in pharmaceutical solutions typically starts at 50 µm and is not reduced with inspection speed as in manual inspection (there are limitations).
3. Wait, what was I trying to find again? The list of different defects tablets or capsules can be quite long, typically it is at least 20 different defects. If the list of defects is long, we (people) will only focus on the few most common types of defects and may forget to search for certain less common defects.
4. We (people) are looking to be constant, even when we shouldn’t be. We unconsciously strive for a constant performance. This means that if we are used (or expected!) to reject about 2 % of the products, we will unconsciously try to reject 2 % without regard to the quality of the batch. If there is a very faulty batch with many defects, we will lower our error criteria, i.e. we will only concentrate on larger errors, just to keep the rejection rate within the expected range. On the other hand, if a batch has more or less no defects, we will feel the need to reject something and will try to find the slightest variations of the products that would normally be accepted.
5. Light defines what we see! In inspection (manual or automatic), the light defines the visibility of various defects. For example, contrast defects (dirts, dots, colors) are well visible in diffuse light, surface defects become visible when the light comes from a low angle, and shape and size measurements are easiest to do with backlight (silhouette view). Manual inspection typically uses only one type of light, diffuse light. This makes manual inspection less sensitive to low-contrast surface defects, such as engraving/embossing inspection, coating defects, etc. On the other hand, the machines can use all light modulations to increase sensitivity to all types of defects.
6. Absolute measurement with eyes? We humans struggle with certain measurements. For example, the absolute size measurement (thickness of the tablet, length of the capsule) cannot be performed with the naked eye. For accurate measurements we need a caliper gage or a microscope with a scale. Such measurement cannot be performed in real time in high volume production. Another example is color. Machines can measure color very accurately in any color space. On the other hand, we can only compare color with another color, meaning, we must always have a reference next to the observed object. In addition, the human perception of color depends on each individual.
7. Imagine people had “save” and “load” function! Machines can be easily configured for high or low sensitivity for the same product. Various sensitivity settings can be saved as recipes. Based on the product and campaign requirements, the corresponding recipe can be retrieved later at any time for a repeatable and reliable inspection. In such instances, i.e. in irregular inspection campaigns, we have to be re-trained or re-introduced to the product and campaign specifics every time.
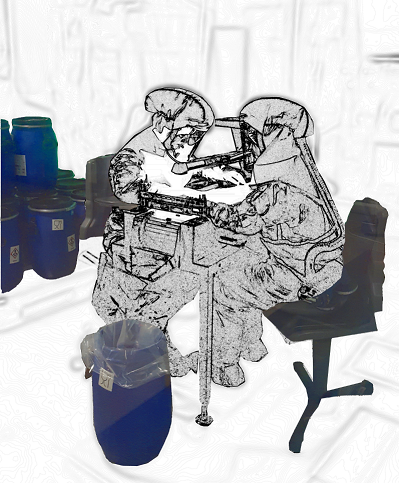
In case of toxic products, workers need additional personal protection equipment for handling of product. It makes the inspection process safer but definitely not easier or faster.
This article was originally published by Miha Možina, PhD, in one of his articles on LinkedIn:
– https://www.linkedin.com/pulse/7-risks-manual-inspection-miha-mozina-phd